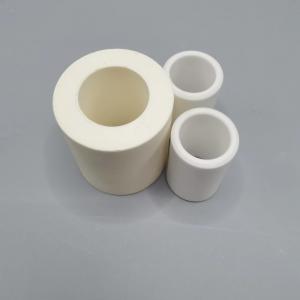
Add to Cart
alumina ceramics tube electronic engineering chemical metallurgy spin electric power corrosion resistance
product name:alumina ceramic tube
The structure of alumina ceramic material is stable. Al2O3 is the main raw material of alumina ceramic, and α-Al2O3 is the main crystal phase, which is the most widely used and the largest output ceramic material in oxide ceramics. In alumina ceramics, the higher the alumina content, the better the performance. Alumina ceramics have the following advantages :
( 1 ) has high mechanical strength and hardness. Its Rockwell hardness is HRA80-90, second only to diamond, far more than wear-resistant steel and stainless steel.
( 2 ) Good wear resistance. Its wear resistance is 266 times that of manganese steel and 171.5 times that of high chromium cast iron.
( 3 ) Good chemical stability, excellent electrical insulation performance, low high frequency dielectric loss, high temperature resistance, chemical corrosion resistance, good thermal conductivity and good biocompatibility.
Because of these excellent comprehensive technical properties, alumina ceramics have been widely used in electronics, electrical appliances, machinery, chemical industry, textile, medicine, automobile, metallurgy, aerospace and other industries. However, there is little research on alumina ceramics in the direction of civil use. Alumina ceramics not only have the above excellent properties, but also have the advantages of high whiteness, high resistance to falling, small sintering shrinkage ( about 10 % alumina in the same forming process, while about 18 % daily porcelain, small product deformation, high yield ), high purity of raw materials, non-toxic, harmless, health and environmental protection. Compared with other daily porcelain varieties, it is a high-quality porcelain variety.
products index:
Ceramic characteristic table | |||
name | 99% AL2O3 | 95% AL2O3 | |
physical propertyessential component | essential component | AL2O3≥99% | AL2O3≥95% |
Density(g/cm3) | 3.85 | 3.6 | |
water absorption% | 0 | 0 | |
sintering temperature | 1690 | 1670 | |
material characters | Hardness(HV) | 1700 | 1600 |
break off strength | >6500 | >2900 | |
compressive strength | 30000 | 25000 | |
thermal response | maximum service tempera- ture | 1500 | 1400 |
thermal expansion coefficient | 8 | 7.8 | |
10-6/℃ | |||
0-1000℃ | |||
Heat shock resistance T(℃) | 200 | 220 | |
thermal conductivity W/m.k | 31 | 22 | |
electrical specification | volume resistivity Ω.cm | >1012 | >1012 |
Insulation destructive power KT/m | 18 | 16 | |
dielectric constant 1MHZ(E) | 9.2-10.5 | 9.0-10 |
Company workshop production pictures: